ARTICLE
The importance of collaboration – part 1
Biologic drugs differ from traditional medicines as they are produced in living systems, making their development and manufacturing more complex. Every stage, from early development to large-scale production, requires precise control due to variables such as cell culture conditions, purification processes, and regulatory requirements.
One major misconception is that a process working in the lab will scale easily to commercial production. Small changes in cell culture, raw materials, or purification can impact yield and consistency. Another false assumption is that process changes can be made late in development without regulatory consequences, which can lead to costly delays.
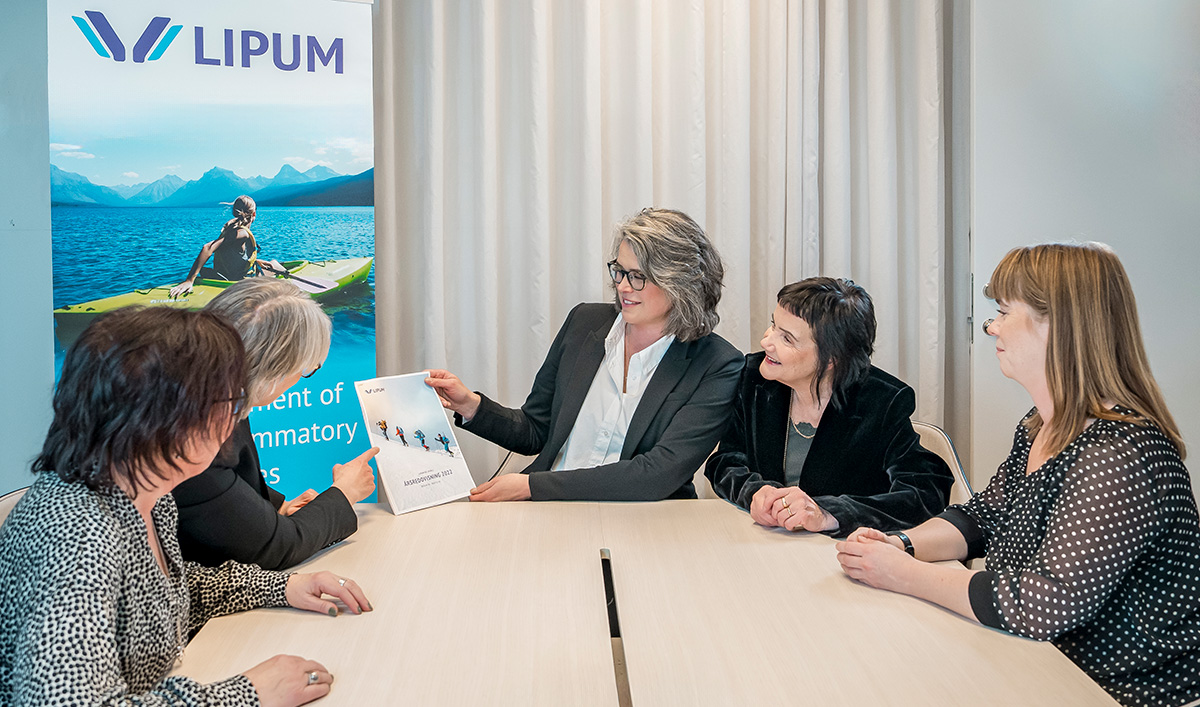
Early collaboration with a Contract Development and Manufacturing Organization (CDMO) is crucial. Engaging a CDMO during preclinical development helps refine processes, align analytical methods, and avoid unexpected issues during scale-up. Delaying this partnership may lead to difficulties in meeting clinical and commercial timelines.
Successful biologic drug development relies on strong collaboration between the developer and owner of the biologic and the CDMO. Working together from the beginning ensures smoother technology transfer, risk mitigation, and regulatory preparedness. Investors should also consider the high upfront costs of biologics, which create barriers to competition but offer long-term advantages through optimized processes and extended market exclusivity.
Case study: SOL-116
Lipum’s SOL-116, a humanized antibody targeting Bile Salt-Stimulated Lipase (BSSL), represents an innovative treatment for inflammatory diseases. Bringing it to market requires overcoming manufacturing challenges such as cell line development, process optimization, and regulatory approval.
Key strategies for maintaining product consistency include robust process control, quality attribute characterization, and stringent raw material qualification. Continuous monitoring and proactive collaboration between Lipum and NorthX Biologics will help navigate these complexities and ensure scalability.
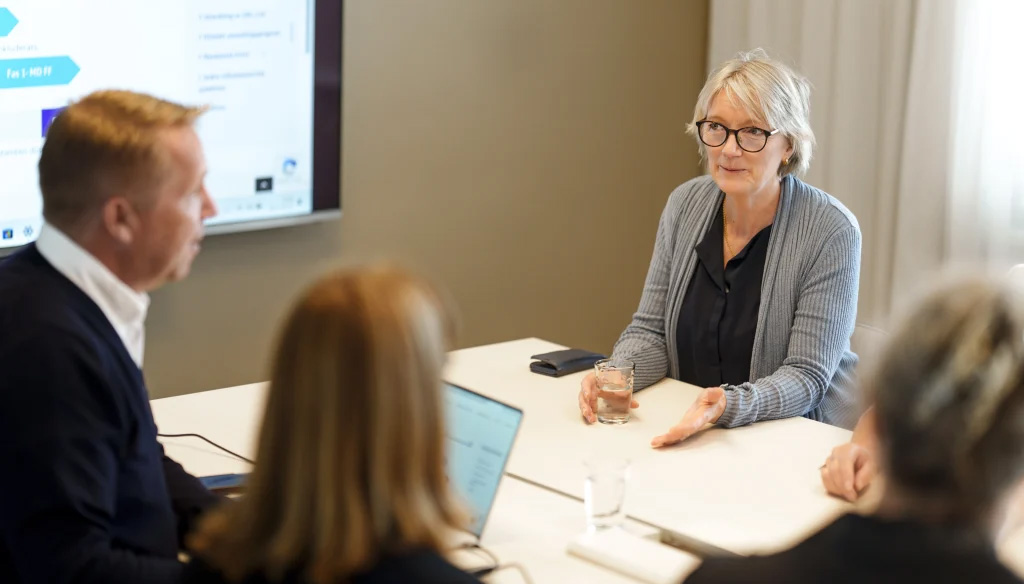
Building a successful partnership
An effective partnership is built on transparency, early alignment of expectations, and shared risk management. Using digital tools for process monitoring, investing in flexible manufacturing, and ensuring knowledge transfer between teams are essential for future biologic innovations. By fostering strong collaboration, companies can improve efficiency, reduce risks, and successfully bring life-changing therapies to patients.