ARTICLE
The critical role of technology transfer – part 2
The journey from early development to commercial production in biologics is paved with complexity and few phases are more pivotal than technology transfer. This step marks the transition of early-stage development to large-scale manufacturing by Good Manufacturing Practice (GMP), and its success is vital for ensuring product consistency, regulatory compliance, and commercial readiness.
For biologic drugs, where minor deviations in process conditions can significantly affect product quality, technology transfer is not just administrative. It’s a collaborative, highly technical process involving the structured exchange of data, methods, analysis, materials, and know-how between the development site and the manufacturing partner.
From development to delivery: The CDMO’s role
NorthX Biologics is a biopharmaceutical CDMO with a rich heritage in Good Manufacturing Practice (GMP) since 1992. With a focus on scientific collaboration and expertise, NorthX Biologics is “Beyond CDMO”, working closely with biopharmaceutical developers to help advance complex biologics from early concept to clinical and commercial stages.
Technology transfer is managed through a cross-functional team that oversees planning, risk assessment, and execution. The goal is not only to reproduce the process but also to future proof it for later clinical phases by optimizing and making it scalable for GMP-compliant manufacturing.
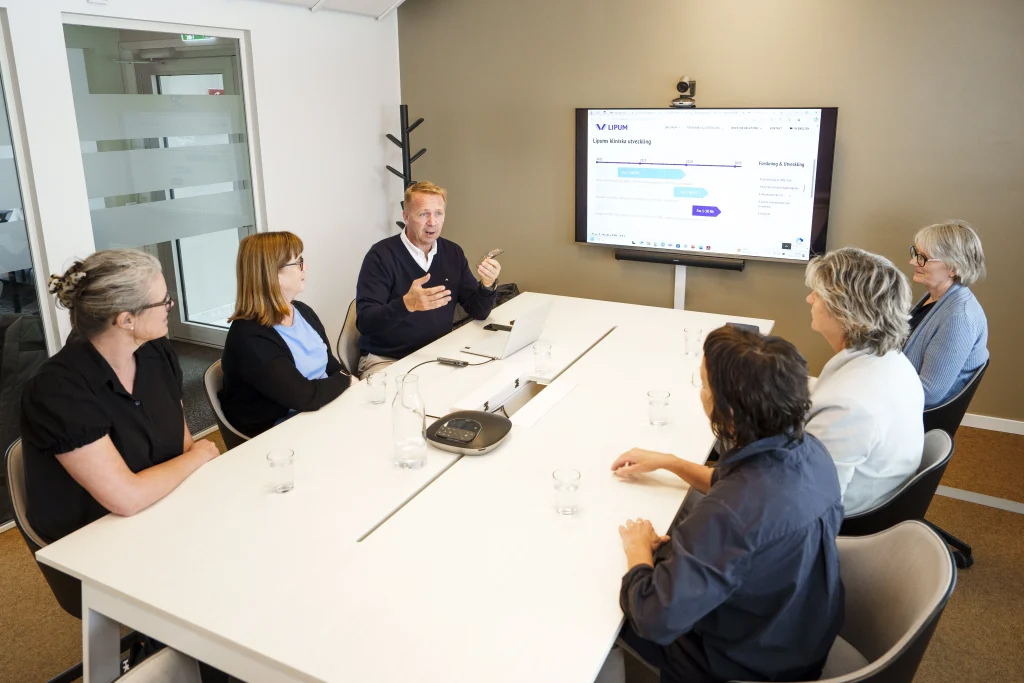
Key steps may include:
- Comprehensive Data Review – Evaluating process descriptions, historical batch data, and analytical methods to ensure completeness and consistency.
- Material Transfer – Handling cell banks, reference standards, and raw materials, with a focus on verifying their integrity and suitability.
- Confirmation Run – Conducting a small-scale production (typically 1–2 L) under NorthX Biologics conditions to test process parameters and identify any necessary adjustments.
- Engineering Batch – A non-GMP engineering batch is executed under GMP-like conditions to simulate full production and evaluating potential scaling and/or transfer effects.
- Documentation Finalization – Developing batch records, control strategies, and specifications aligned with GMP requirements.
Even with thorough preparation, subtle differences between development and manufacturing environments often surface during the engineering run. Early collaboration helps mitigate these by aligning expectations, refining methods, and building mutual understanding.
Preparing for the next phase
For Lipum, technology transfer is more than a procedural handoff. It’s a chance to reassess and refine the manufacturing strategy. As the process transitions from one GMP manufacturing site to another, even well-established procedures are challenged by differences in equipment, systems, and interpretation of standards, often uncovering areas for refinement and alignment.
This phase also strengthens collaboration. Clear communication, shared risk ownership, and proactive problem-solving set the stage for a smoother path to future commercialization. A thoughtful approach now helps secure a reliable and efficient manufacturing platform for the future.
Ensuring a robust and scalable process
A successful technology transfer results in a process that is both reproducible and robust, a process able to withstand the scale-up to volumes without compromising quality. This requires a deep understanding of critical process parameters (CPPs), well-defined quality attributes, and validated analytical methods.
While the confirmation and engineering runs play a vital role in uncovering issues early, the work doesn’t end there. Continuous collaboration enables iterative improvements and ensures the process evolves in tandem with clinical and regulatory milestones. Transparency, shared ownership, and a commitment to quality form the foundation of a successful long-term partnership.
Looking ahead
As the process moves toward full-scale GMP production, the lessons learned during technology transfer will continue to shape the manufacturing strategy. By focusing on precision, partnership, and proactive planning, companies can bridge the gap between innovation and execution and bring promising biologic therapies closer to the patients who need them most.